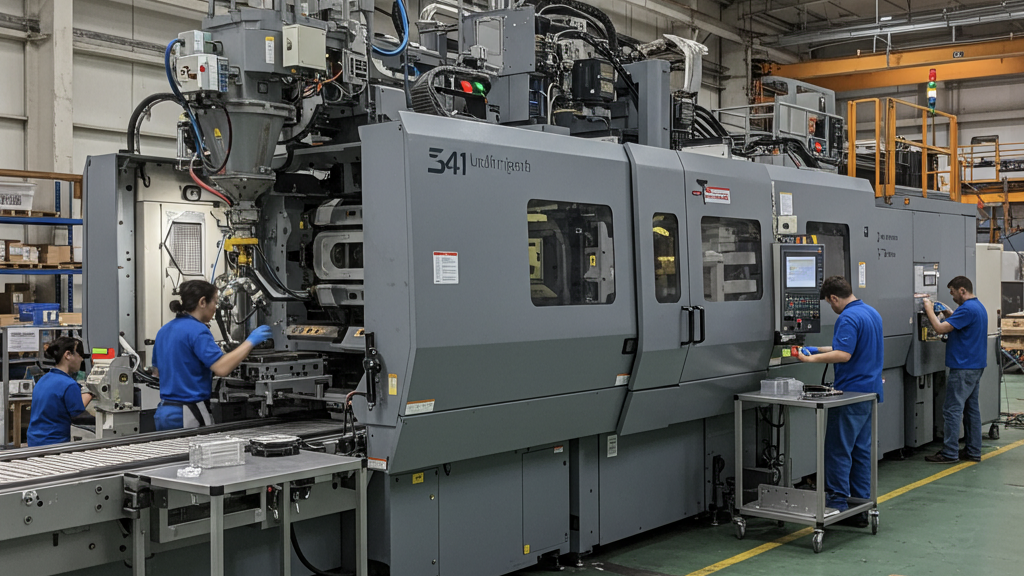
Injection molding release is a critical part of production, affecting product quality and cost. Demoulding challenges such as sticking and deformation, reducing efficiency and wasting material. Efficient and non-destructive demoulding is an urgent problem for enterprises to solve. This article will explore the influencing factors and provide solutions.
How can this knowledge be used in practice? We will explain specific strategies in terms of mold optimization, release agents, process control, and more. Combined with practical cases, provide actionable guidance.
What are the key factors for release efficiency and quality?
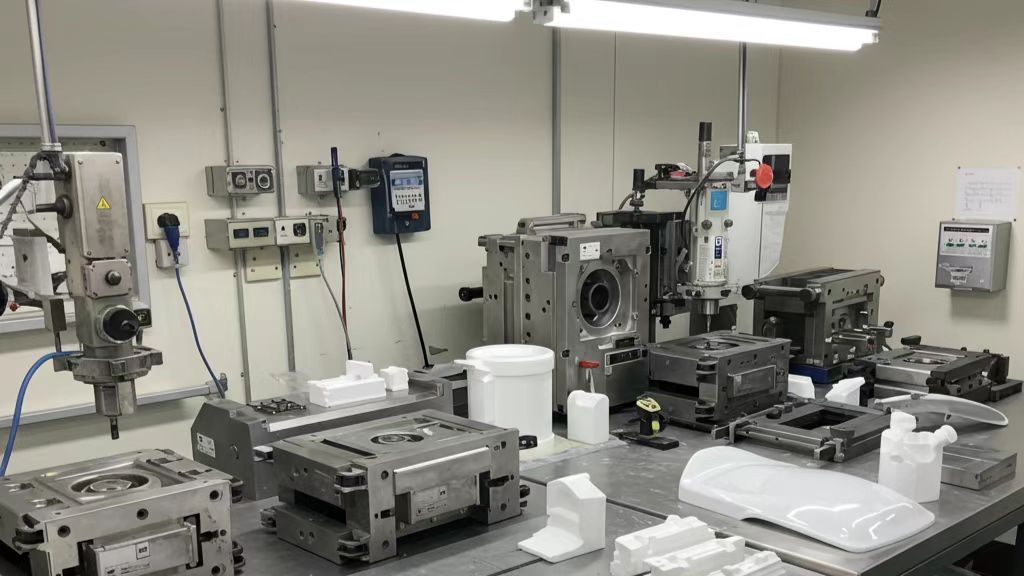
In the injection molding demolding process, efficiency and quality are affected by a number of key factors. Considering the following key factors, we can effectively improve the efficiency and quality of injection mold release, reduce production costs, and improve product quality.
- Mold design: Reasonable mold design, including demoulding slope, ejection system and surface treatment, is the basis for smooth demoulding.
- Material selection: Choose materials with good fluidity and low shrinkage, which can effectively reduce the difficulty of demoulding.
- Process parameters: Precise control of injection pressure, speed, mold temperature and cooling time to optimize the release effect.
- Application of release agent: Proper selection and application of release agent can reduce product adhesion to the mold.
How can I optimize my release process and reduce defects?
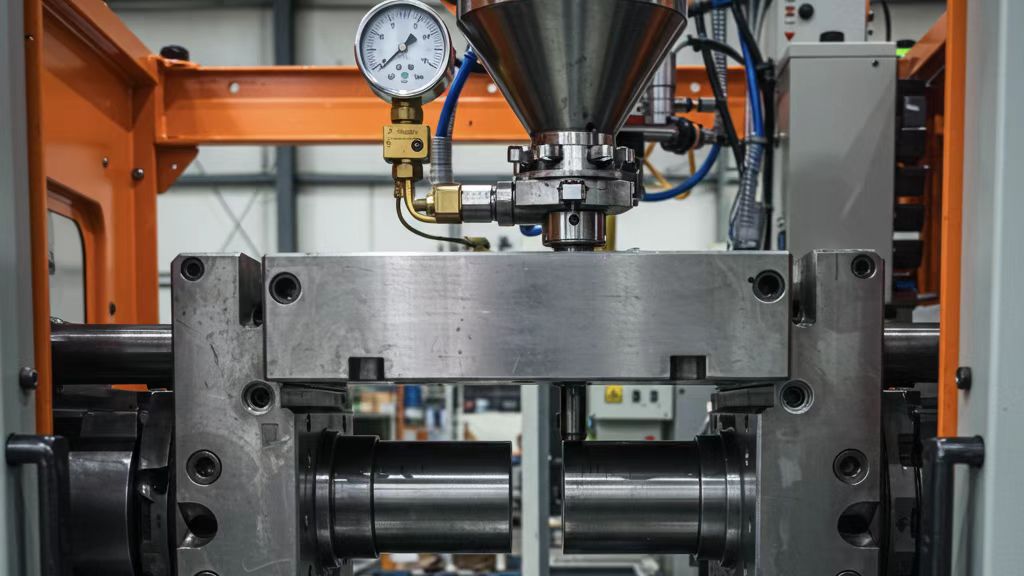
Optimizing the demoulding process and reducing defects is a complex process that involves many factors. The combination of these strategies can effectively optimize the demoulding process, reduce product defects, and improve production efficiency and product quality.
- Mold optimization: By optimizing the mold design, such as the demoulding slope, ejection system, and surface treatment, the release quality can be significantly improved.
- Process parameter control: Precise control of process parameters such as temperature, injection pressure, and cooling time is key to reducing product defects.
- Material selection and treatment: Selecting the right material and pre-treating it can reduce the difficulty of demoulding and the probability of defects from the source.
- Automatic demoulding technology: The application of automatic demoulding technology can improve the efficiency and stability of demoulding and reduce the defects caused by man.
What is the future trend of mold release technology?
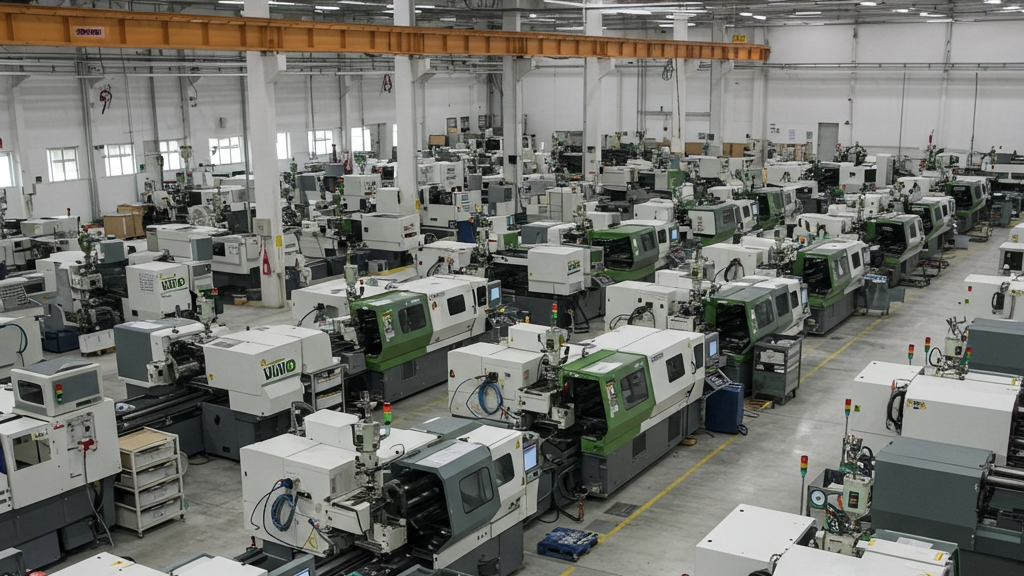
With the continuous development of science and technology, injection molding release technology is also constantly improving. In the future, the release technology will be more intelligent, automated, environmentally friendly and precise to meet the growing production needs and environmental protection requirements.
- Intelligence and automation: Through intelligent monitoring and automation system, the optimization of the demoulding process and unmanned production are realized.
- Environmental protection and sustainability: Promote the application of environmentally friendly release agents, energy conservation and emission reduction, and achieve green and sustainable production.
- High-performance materials and technologies: research and development of new release materials and application of advanced mold technology to improve mold release efficiency and product quality.
- Precision and personalization: Achieve precise demoulding and personalized customization to meet the needs of different products and customers.
Comparison of advantages and disadvantages of injection mold release
Demoulding technology |
merit |
shortcoming |
Applicable scenarios |
Conventional ejection and demoulding | Low cost and simple maintenance | It is easy to deform and has low efficiency. | Simple product, low yield. |
Demoulding of the manipulator | High automation, high efficiency and low damage. | High cost and programming required. | High-volume, complex products. |
Release agent application | Reduces sticking mold and improves surface quality. | It needs to be applied regularly, which may affect the subsequent processing. | A wide range of products, especially complex shapes. |
Intelligent demoulding | Real-time monitoring, intelligent control, improve quality. | The cost is high and the technical requirements are high. | High-end products, high-demand production. |
The effect of demoulding on product quality
Mold release is a very important part of injection molding production, which is directly related to the quality of the final product. Optimizing the release process and selecting the right release technology and materials is essential to ensure product quality.
1.Product deformation and damage: Improper demoulding force will cause the physical form of the product to change, such as bending or rupture, which directly affects the structural integrity of the product.
2.Surface defects: Friction or release agent residue during the demoulding process will cause scratches, dents and other defects on the surface of the product, reducing the appearance quality.
3.Dimensional accuracy: The deformation and shrinkage during demoulding will cause the product size to deviate from the design standard, affecting the product assembly and functional realization.
4.Internal stress: The uneven demoulding force will produce residual stress inside the product, which will affect the stability and durability of the product for long-term use.
conclusion
The release technology directly affects the quality of injection molding products. Improper demoulding can easily cause product deformation, surface defects and dimensional deviations. Optimizing the demoulding process can significantly improve the performance and appearance of the product. Enterprises should pay attention to demoulding technology to ensure product quality and market competitiveness.
For expert assistance in implementing for your production needs, visit our resource center or contact us. Let’s help you scale up your manufacturing with precision and efficiency!
Post time: Mar-04-2025